The recyclability of concrete as an aggregate
Recycling is starting to play a larger and larger role in our everyday lives. Even in the field of construction we often encounter the selective collection and the re-use of construction and demolition waste.
One good example is the management of the waste coming from the demolition of the Magasház in Pécs, which resulted in 22.549 tons of debris [1]. In Hungary selectively collected concrete waste is mainly used in filling and road construction, although a large part of it would be suitable as an aggregate as well. The European Aggregates Association (UEPG) prepares annual statistics on the production of various additives of 39 countries, including Hungary [2]. According to their estimation in 2015 58 million tons of aggregate was produced in Hungary, of which only 3.4% was recycled aggregate (Table 1). This statistics shows that the neighbouring countries are similarly poor or even worse in manufacturing and using recycled aggregates. The examples of England, Belgium, the Netherlands or Germany point out to us that there is much room to improve in this area.
Table 1: Estimated amount of different aggregates produced in 2015 (based on UEPG’s statistics)
Estimated amount of aggregates produced in 2015 (million tons) | ||||||||
---|---|---|---|---|---|---|---|---|
Country | Sand and gravel | Crushed stone | Marine | Recycled | Recycled on-site | Manufactured | Total | Recycled/total |
England | 49 | 121 | 12 | 52 | 2 | 12 | 248 | 21,0% |
Austria | 63 | 33 | 0 | 4 | 0 | 2 | 102 | 3,9% |
Belgium | 13 | 45 | 6 | 15 | 0 | 1 | 81 | 18,5% |
Netherlands | 50 | 0 | 12 | 18 | 0 | 0 | 80 | 22,5% |
Croatia | 4 | 15 | 0 | 0 | 0 | 0 | 20 | 0,0% |
Hungary | 40 | 16 | 0 | 2 | 0 | 0 | 58 | 3,4% |
Germany | 231 | 207 | 10 | 68 | 0 | 29 | 545 | 12,5% |
Romania | 55 | 34 | 0 | 0 | 0 | 0 | 90 | 0,0% |
Slovakia | 10 | 18 | 0 | 0 | 1 | 0 | 30 | 0,0% |
Slovenia | 3 | 8 | 0 | 0 | 0 | 0 | 11 | 0,0% |
In addition to environmental aspects this demand is increasingly reinforced by the shortage of aggregates due to the sudden boost of the concrete industry. These days obtaining the right quality aggregate, which could be partly replaced by recycled aggregates, is starting to pose a major problem nationwide. Previously the main obstacles in this area were inadequate regulations and unsatisfactory professional experience. To remedy the situation the Hungarian department of fib, (the International Federation for Structural Concrete) prepared a directive back in 2005 entitled “The production of concrete with the recycling of waste coming from demolition, construction and building material manufacture” [3], which is still regarded as useful literature for those who are interested in the subject.
Since then the new MSZ 4798:2016 standard and 1M and 2M standard modifications were also issued. These cover the subject of recycled concrete as well. (According to the standard we are speaking of recycled concrete if it contains recycled aggregate or the aggregate content contains more than 5% by weight reclaimed aggregate. The reclaimed aggregates are separated into two categories: aggregate reclaimed from fresh concrete after washing treatment, and reclaimed aggregate produced by the crushing of hardened concrete unused in the construction process.) Thus this standard provides at least limited opportunities for recycling demolished concrete as aggregate.
The lack of professional experience, however, is a serious problem up to this day. Recycled concrete has an image that says it always possesses poorer characteristics than concrete made with traditional aggregates. Any damaging effect, however, can be prevented with proper caution. In the cases of recycled and reclaimed aggregates the regular examination of materials and the careful planning of the composition hold much more serious roles as opposed to working with traditional aggregates. It is possible to manufacture concrete with the proper recycled and reclaimed aggregates that has the same, or even better qualities than concrete made with traditional aggregates.
We conducted an experiment to analyse the effect of completely replacing the coarse fraction (4/16) of sandy gravel aggregate of natural origin with good quality reclaimed, crushed aggregates. The reclaimed, crushed aggregate was made by breaking down 2-year old concrete sample cubes. The sample cubes used for aggregate had an edge length of 150 mm and an average bulk density of 2407 kg/m³ during the recycling process, while their average compressive strength was 76,2 N/mm². (The reclaimed, crushed aggregate was created with a jaw crusher, double crushing and dry separation.)
The concrete composition used in the experiments is shown in Table 2. The concrete was stirred for five minutes in order to reach homogenous mixing. By varying the amount of the plasticizing additive a consistency class F4 was set for each blend. In certain blends we also used fibres, which were in every case added after stirring the fresh concrete. After adding the fibre we stirred the fibre-containing concretes for an additional five minutes.
Table 2: Concrete composition used in the experiments
Material | Type | Mass (kg/m³) |
---|---|---|
Aggregate | 0/4 mm fraction (45%): natural sand | 824 |
4/16 mm fraction (55%): natural gravel or reclaimed crushed concrete | 1008 | |
Total (100%) | 1832 | |
Cement | CEM I 42,5 N (Duna-Dráva Cement) | 380 |
Water | mw/mc= 0,43 | 163 |
Additive | polycarboxylate ether-based plasticizer | max. 0,7 mc % |
Fibre | steel fibre and polymer macrofibre | 0,5 V % |
Table 3 shows that by using the proper, reclaimed crushed aggregate a higher compressive strength was achieved as opposed to using traditional classified sandy gravel. (In Table 3 mixtures made with classified sandy gravel are marked SG, while mixtures using sand and reclaimed, crushed aggregate are marked REC.) Our test results have proven that with the right material and care the qualities of recycled concrete could be similar or even better than concrete made with traditional aggregates.
Table 3: Average compressive strength and bulk density at 90 days (all result averaged three measurements)
Sample sign | Compressive strength(N/mm2) | Bulk density ( kg/m3) |
---|---|---|
SG without fibre | 91,34 | 2382,02 |
REC without fibre | 99,13 | 2357,61 |
SG-steel fibre-0,5V% | 74,19 | 2286,14 |
REC-steel fibre-0,5V% | 100,56 | 2297,27 |
SG-polymer macrofibre-0,5V% | 88,88 | 2355,69 |
REC-polymer macrofibre-0,5V% | 101,57 | 2283,48 |
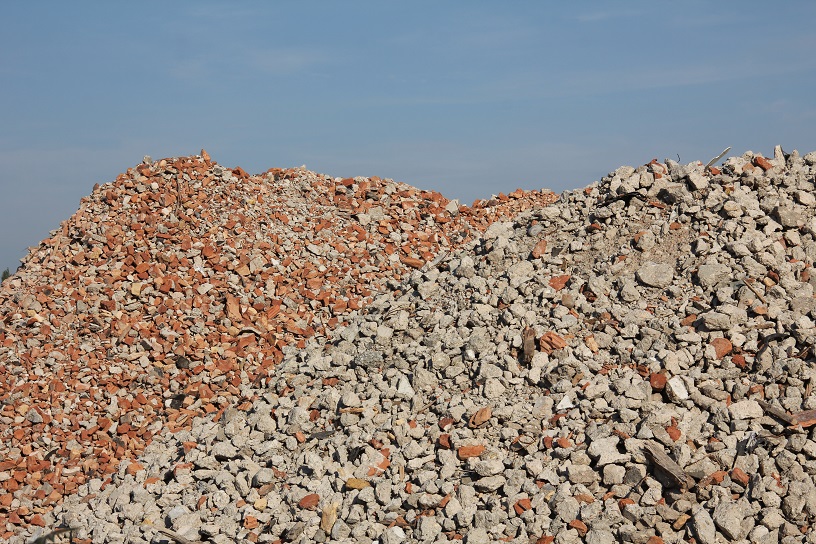
Recycling of building materials waste.
Beton Technológia Centrum Kft.
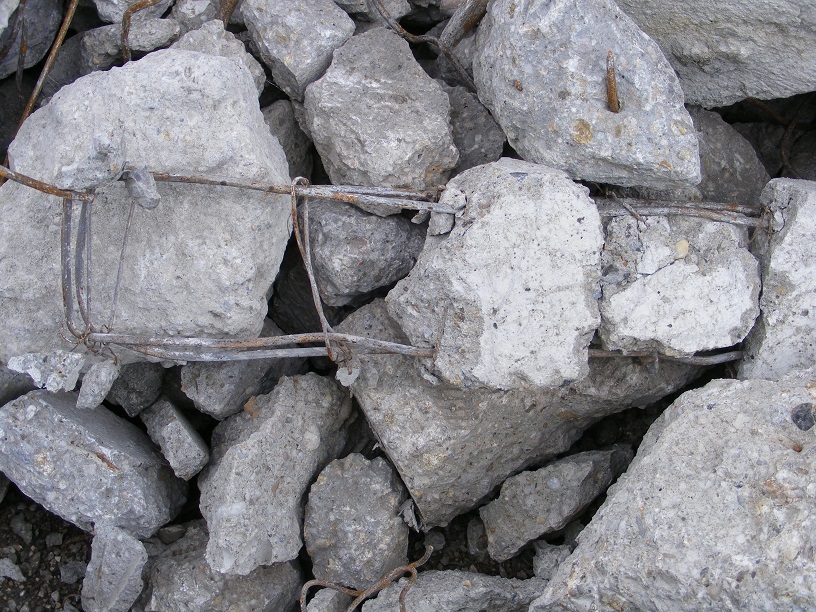
Recycling of construction waste.
Beton Technológia Centrum Kft.
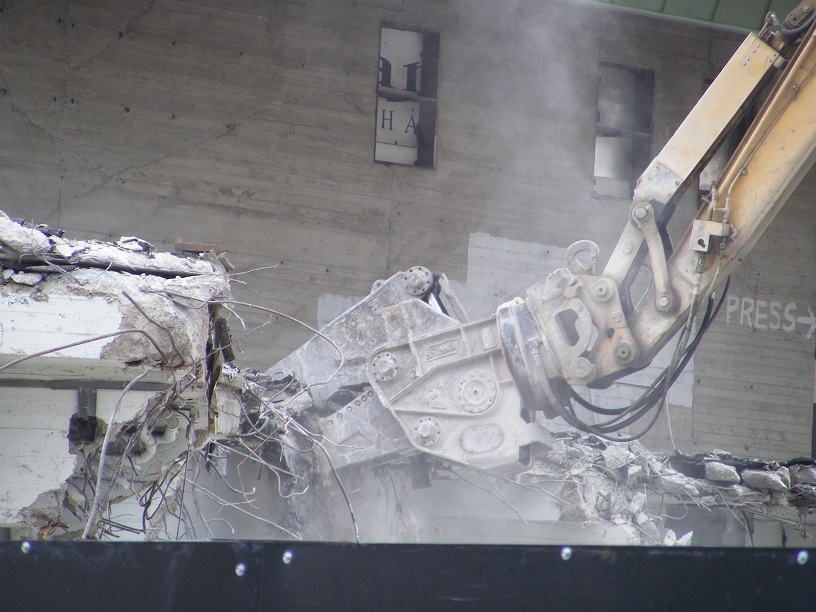
Recycling of demolition waste.
Beton Technológia Centrum Kft.
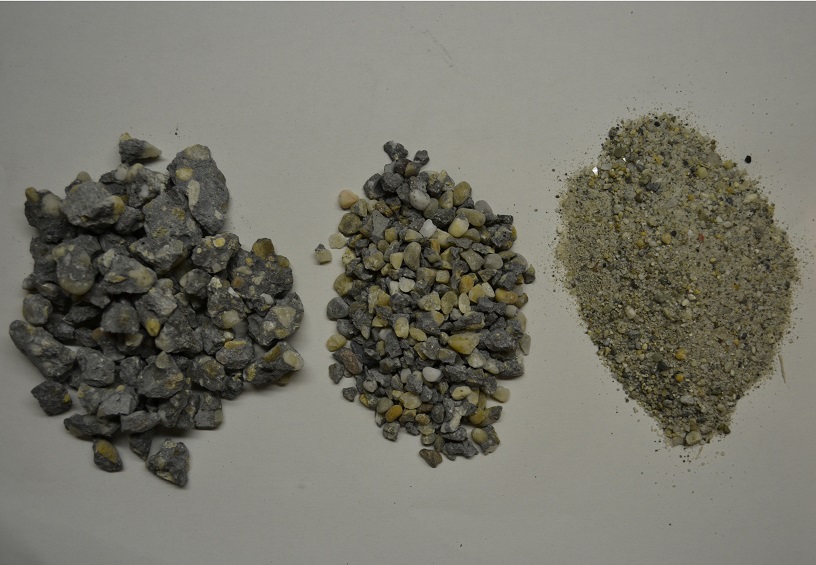
Additive.
Beton Technológia Centrum Kft.
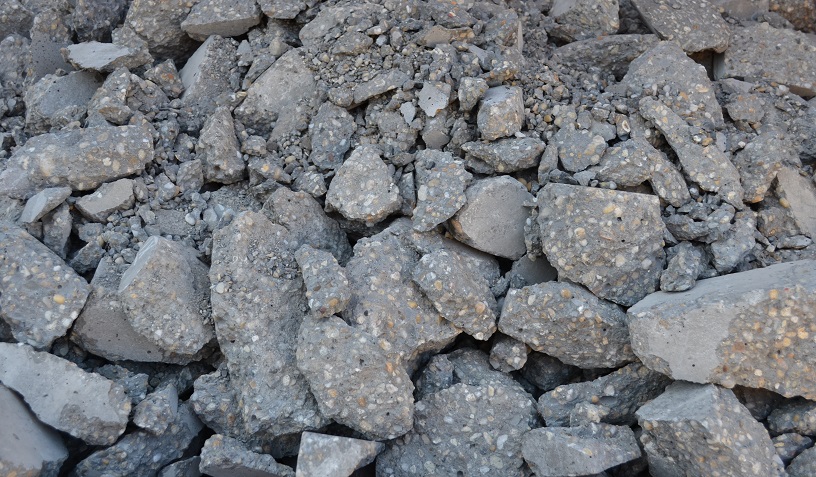
Debris.
Beton Technológia Centrum Kft.
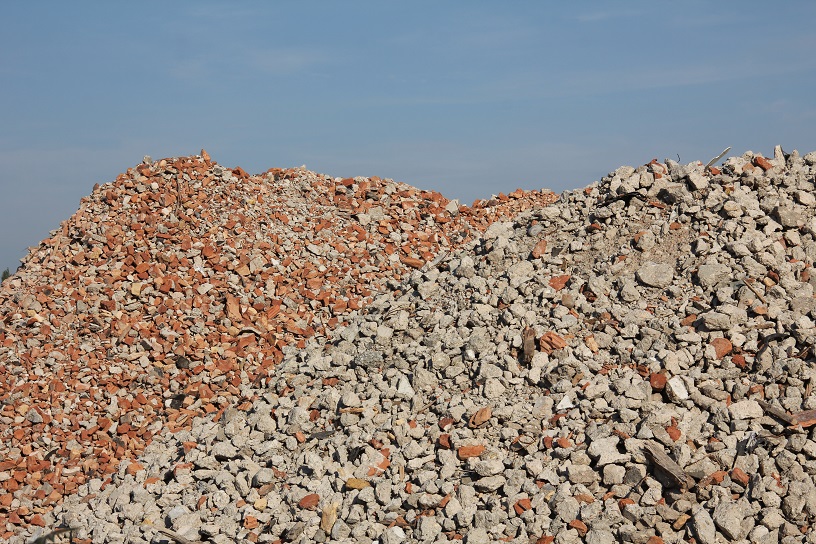
Recycling of building materials waste.
Beton Technológia Centrum Kft.
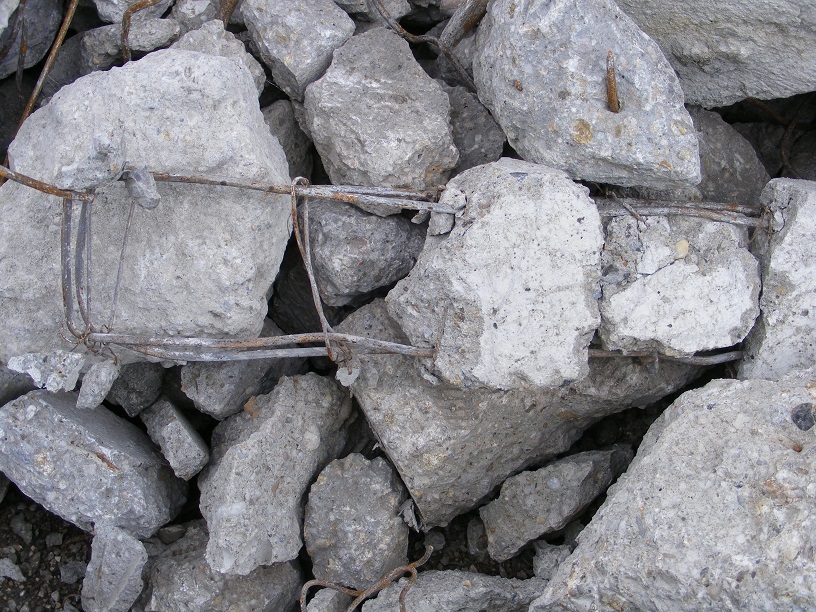
Recycling of construction waste.
Beton Technológia Centrum Kft.
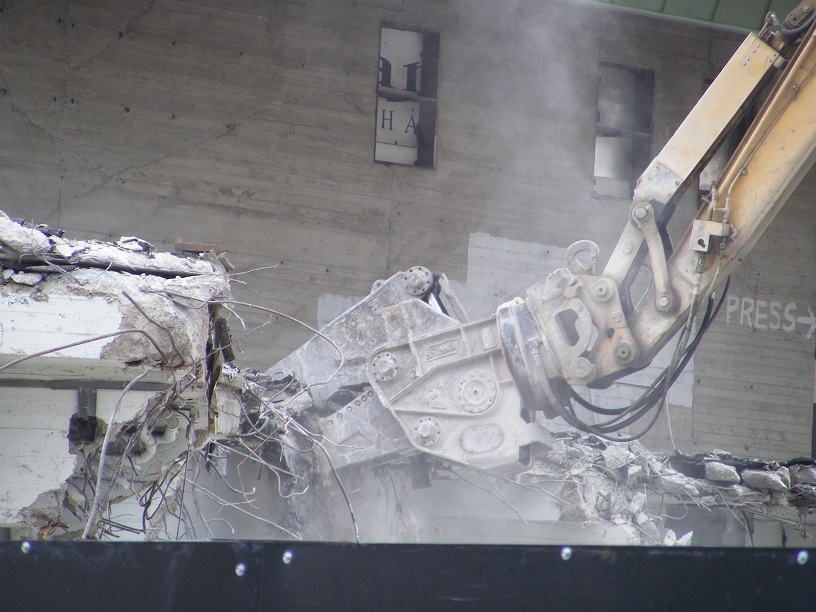
Recycling of demolition waste.
Beton Technológia Centrum Kft.
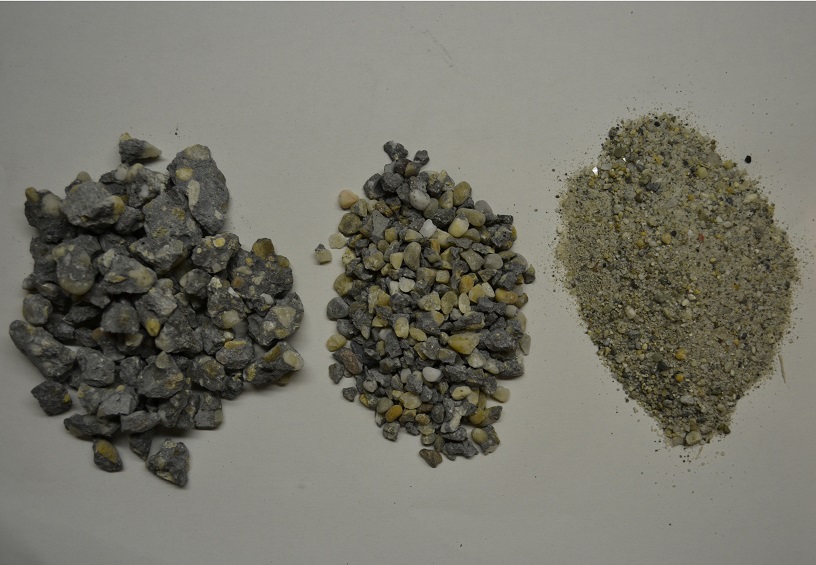
Additive.
Beton Technológia Centrum Kft.
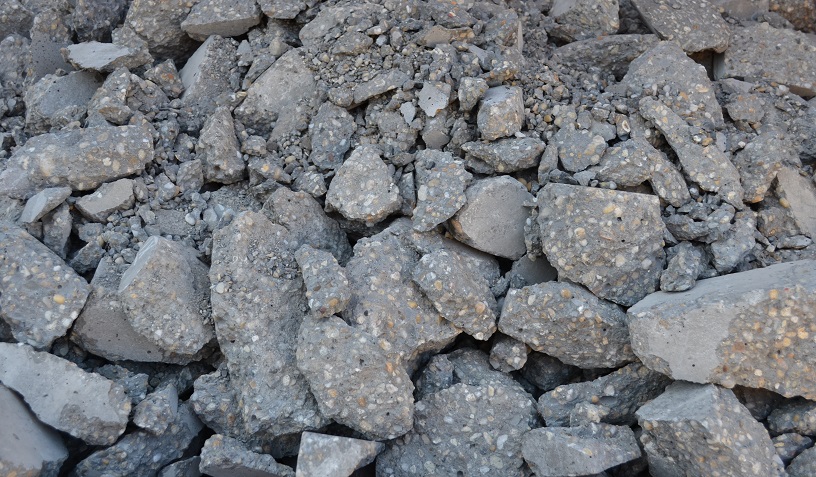
Debris.
Beton Technológia Centrum Kft.